Listen to this article
Introduction
Tunnel ventilation originated in the poultry industry and later spread to the swine and dairy industries. Today, tunnel ventilation is a common type of mechanical ventilation used in dairy barns. Tunnel ventilation involves using fans placed in one gable endwall of a building and inlets placed in the opposite gable endwall to create a continuous flow of air through the barn’s length. For tunnel ventilation to function efficiently, all sidewall, ceiling, and floor openings must be sealed to create the “tunnel” effect.
Tunnel ventilation is often compared to cross ventilation. While tunnel ventilation is effective in long and narrow barns, cross ventilation is ideal for wide barns with shorter lengths. Sprinklers are often used in tunnel ventilation to increase the evaporative cooling effect. The choice between the two depends on the barn layout and specific ventilation requirements.
Why do we need ventilation systems?
Dairy cattle need a consistent fresh, clean air source to maximize their production potential. Hot, stale air adversely affects milk production and milk quality. To achieve proper barn ventilation, air from within the barn needs to be exchanged with fresh air from outside the barn.
Limitations of a Tunnel Ventilation System?
Tunnel ventilation works well in the hot months of summer. However, it is generally not an appropriate ventilation system for use during the colder winter months. The air speeds associated with a well-designed tunnel system can result in cold, drafty conditions when operated in the winter.
The length of the barn is also a limitation with this system. As the fresh air travels the length of the barn, it is contaminated with air pollutants. At some point, the air that was brought in by the inlet is no longer considered “fresh” and provides limited benefits to the cows past this point. Therefore, the optimal length of a dairy barn using tunnel ventilation is 300 – 400 feet.
Airflow inside tunnel-ventilated buildings
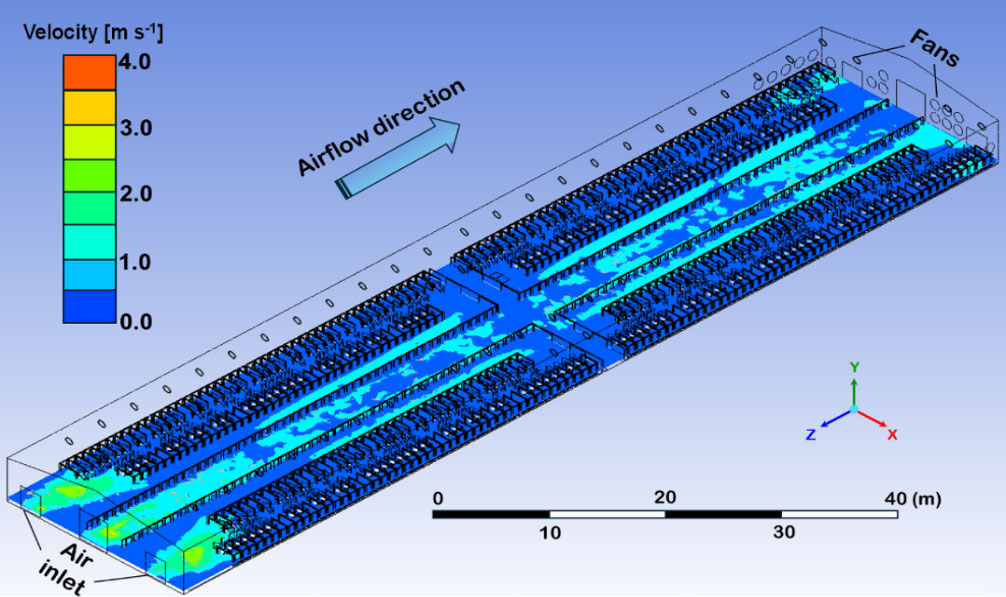
Computational simulations are often used by researchers to understand how a ventilation system performs. In the simulation above, the velocity profile of a tunnel-ventilated building is shown. Cows are in their stalls (some standing and others resting), and the exhaust fans draw air perpendicular to the stalls. Dark blue areas indicate an airflow rate ranging from 0 to 0.5 m/s, while aqua or light green areas represent higher velocities ranging from 1.0 to 2.5 m/s. In a building with tunnel ventilation, air easily travels through the feed alley, but does not necessarily aerate the stalls. Circulation fans are used to improve the aeration of the stalls and provide cows resting in their stalls with adequate fresh air.
Computational simulations
Computational tools allow us to simulate conditions inside dairy buildings. Once we develop and validate a model, we can test various hypothetical scenarios without needing to fabricate the actual design we want to test.
Our simulations help us visualize airflow in dairy buildings and enhance our understanding of how various ventilation designs may impact air circulation, particularly in areas where cows are resting.
Fan Safety
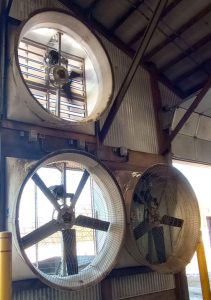
Large fans used in tunnel ventilated barns are usually belt-driven by multiple horsepower motors and have heavy-duty metal or aluminium blades. Contact with these blades is very dangerous! Care must be taken to eliminate the potential for contact between humans and cows. Removable screens, usually available from the manufacturer, should be installed on both the inflow and outflow sides of the fans. Additional space should also be provided between the cows and the fan inlets for maintenance and enhanced safety.
Fan Controls
Since air conditions vary throughout the year, controls should be installed to adjust the tunnel fans to accommodate these changes. There are different systems for controlling the fan function.
Manual Control
Manual control requires frequent attention by a person who has been trained in the operation of the tunnel ventilation system. Changing weather conditions can require frequent or abrupt changes in fan operation and may happen when a trained operator is not available. For this reason, farms may choose to utilize automatic controls.
Automatic Control
Automatic controls are more reliable from a day-to-day perspective. However, you must ensure that you perform preventive maintenance to maintain proper, continuous operation. With an automated system, sensors need to be located at the cow level so they “sense” the air the cows are in contact with. It is also important to ensure that the sensors are not placed in areas where they are affected by solar radiation or extreme localized conditions.
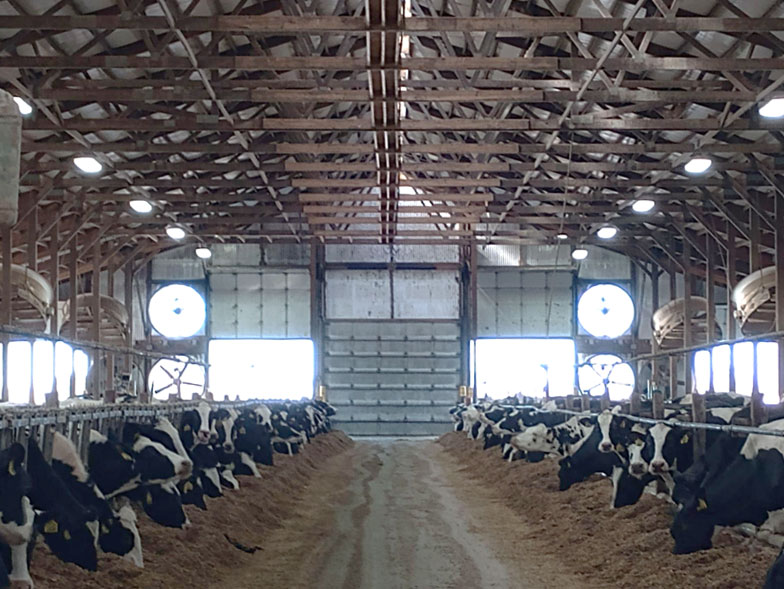
Winter Management
Since tunnel ventilation is not used during winter, an alternate means of providing air exchange is needed. Natural ventilation is a logical choice for this. Natural ventilation requires curtain sidewalls to act as air inlets and air outlets. These sidewalls can also play a role in tunnel ventilation in barns where velocity distribution is non-uniform. Opening the sidewalls 2 inches from the bottom allows a small amount of air to enter along the length of the barn at cow level.
Baffles and Circulation Fans
Barns with high ceilings tend to have large amounts of air movement close to the ceiling. The initial air that enters the barn is at cow level; however, when it collides with the cows, it rises to go past them. Once the air rises, if nothing is there to send it back down, it stays at the ceiling. Circulation fans and baffles help to deflect the air back down towards the cows. If using circulating fans, they should be spaced no more than ten times their diameter apart. Baffles should be spaced 40 – 80 ft apart.
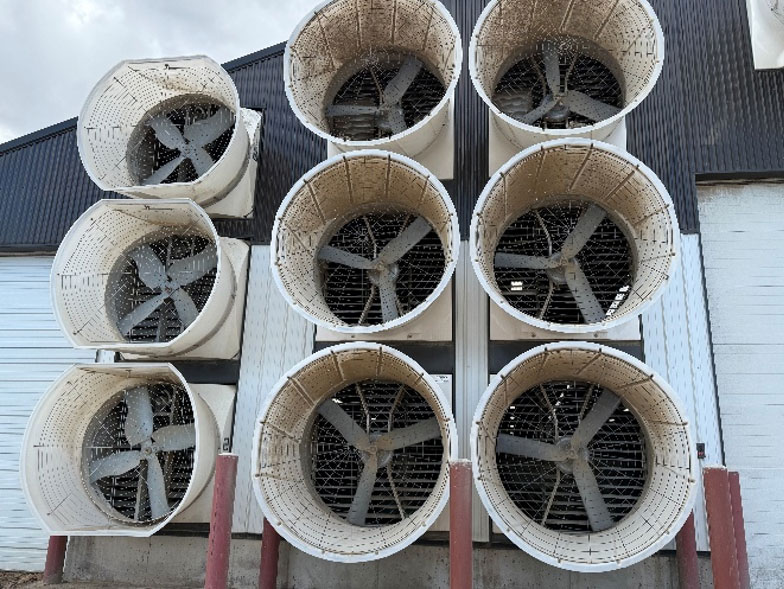
Summary
Tunnel ventilation enhances cow comfort and productivity during hot months by providing consistent airflow. However, it has limitations in winter and in barns over 40 feet long. Proper design, including circulation fans, baffles, and automated controls, ensures effective air distribution at the cow level. During colder months, natural ventilation using sidewall curtains is essential. With thoughtful planning and maintenance, tunnel ventilation can be a valuable system for modern dairy operations.
Authors
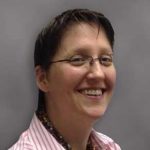
Heather Schlesser
County Dairy Educator – Heather Schlesser is an Agriculture Educator in Marathon County. Heather’s research and outreach have included the use of current technology to enhance farm profitability and sustainability. Her current projects include the Animal Wellbeing Conference, the Midwest Manure Summit, Beef Quality Assurance, financial programming, and teaching farmers throughout the Midwest how to breed their own cattle.
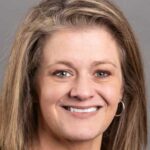
Aerica Bjurstrom
Regional Dairy Educator – Aerica’s work focuses on herd health and animal welfare. She also has a strong background in meat quality and has done programming in market cow carcass quality.
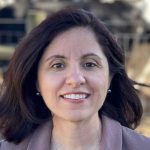
Neslihan Akdeniz
Livestock Controlled Environments Extension Specialist, Assistant Professor– Mainly focusing on controlled environments for livestock production, also interested in nutrient management and indoor plant-growing facilities.
Acknowledgement
We are grateful for the Wisconsin Idea Collaboration grant provided by UW-Madison Extension (AAM9947).
References
- Tunnel Ventilation for Freestall Barns. Gooch, Curt A., Timmons, Michael B.(2000). Cornell University. https://ecommons.cornell.edu/bitstreams/f4338671-8018-448e-88f6-182e608850b6/download
- Tunnel Ventilation for Tie Stall Barns. Tyson, John T., McFarland, Dan F., Graves, Robert E. (2022).Penn State Extension. https://extension.psu.edu/tunnel-ventilation-for-tie-stall-dairy-barns#:~:text=Research%20and%20experience%20indicates%20that,Locating%20fans%20and%20inlet
Download Article